hijacker
Well-Known Member
Ok, I have discovered a pretty big problem with my '94. :real mad:
Last year it developed a small oil leak at the bottom of the Crankcase Cover 2 or Secondary Gear Cover.
Thought to myself: no problem, I'll just replace the gasket. Much to my horror when I pulled the cover off the lobe for the bottom-most bolt was broken off. Had been previously because there was not aluminum pieces or debris present. You can see the broken area in the picture with round green circle around it.
So, attempts to fix the leak have been unsuccessful. I've tried just a gasket, a gasket and permatex and a thick layer of permatex with no gasket. :bang head:
I've spoken with a few people and everyone has suggested that a good next step would be to try to rebuild the missing lobe with a product such as JB Weld Steel Stick. Drill it and tap it.
In order to do this I really need to remove the plate that secures the bottom of the bearing in place. The bolts that hold that plate on have been punched so they are secured in place (see the red arrows in the picture pointing to the bolts I'm referring too).
So, I have 2 questions:::
1. does anyone have a better suggestion other than trying to rebuild the lobe with Steel Stick? Other than replacing the case half or welding.
2. How the heck do I remove those punched bolts? Just sheer force? Do I grind off the punched part of the bolt head?
Help guys!!! :th_help:
Last year it developed a small oil leak at the bottom of the Crankcase Cover 2 or Secondary Gear Cover.
Thought to myself: no problem, I'll just replace the gasket. Much to my horror when I pulled the cover off the lobe for the bottom-most bolt was broken off. Had been previously because there was not aluminum pieces or debris present. You can see the broken area in the picture with round green circle around it.
So, attempts to fix the leak have been unsuccessful. I've tried just a gasket, a gasket and permatex and a thick layer of permatex with no gasket. :bang head:
I've spoken with a few people and everyone has suggested that a good next step would be to try to rebuild the missing lobe with a product such as JB Weld Steel Stick. Drill it and tap it.
In order to do this I really need to remove the plate that secures the bottom of the bearing in place. The bolts that hold that plate on have been punched so they are secured in place (see the red arrows in the picture pointing to the bolts I'm referring too).
So, I have 2 questions:::
1. does anyone have a better suggestion other than trying to rebuild the lobe with Steel Stick? Other than replacing the case half or welding.
2. How the heck do I remove those punched bolts? Just sheer force? Do I grind off the punched part of the bolt head?
Help guys!!! :th_help:
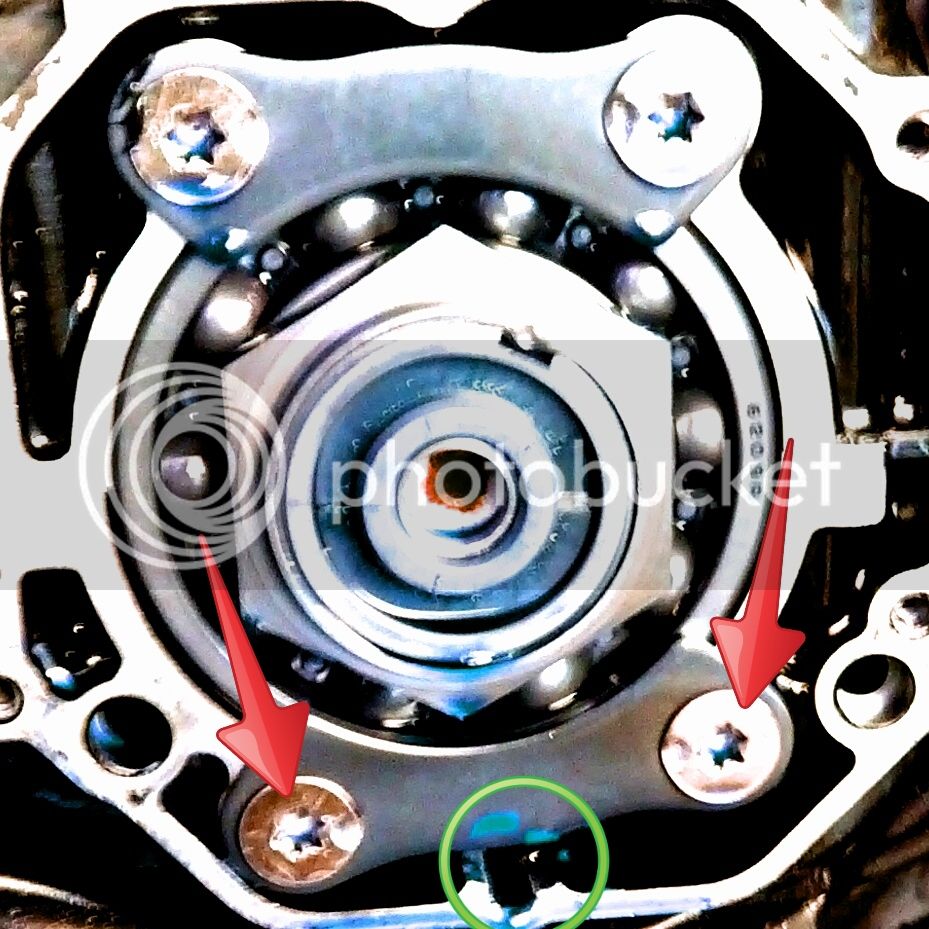